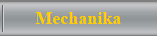 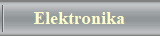 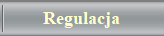
Jakiś czas temu na łamach mojej strony 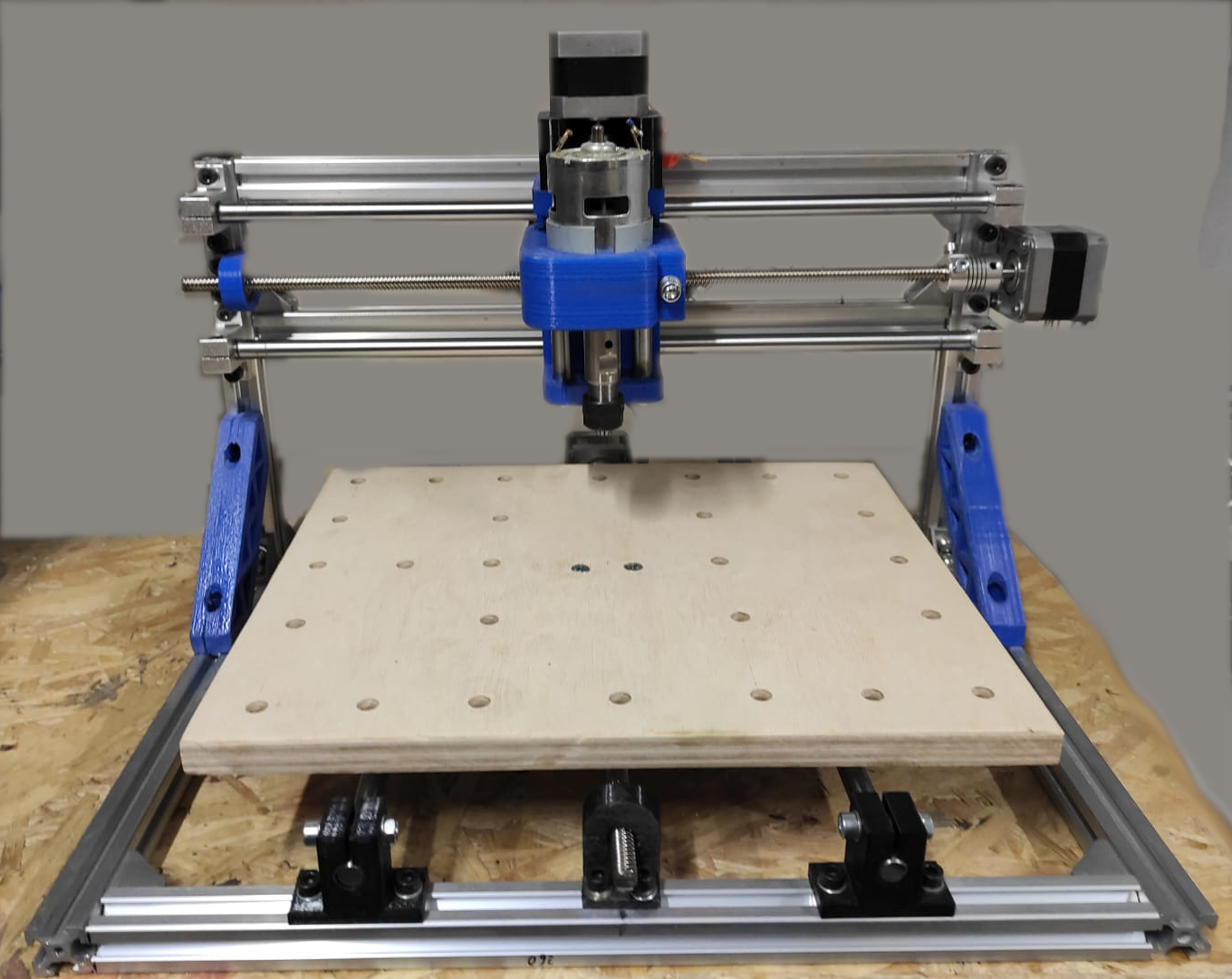 opisałem proces tworzenia CNC mojego prostego projektu. Cel jaki mi wtedy przyświecał był związany przede wszystkim z pragnieniem poznania tej technologii która bardzo mnie fascynuje. W sumie cel został osiągnięty ponieważ maszyna ruszyła, i od tamtej pory przydała mi się w realizacji moich projektów związanych głównie z produkcją obudów oraz innych drobiazgów które raczej trudno byłoby mi wykonać ręcznie zachowując taką precyzję. Poza tym przy okazji podszkoliłem się w obsłudze oprogramowania do realizacji wydruków oraz liznąłem trochę tematu związanego z narzędziami oraz materiałami jakie dane było mi obrabiać. Przy okazji wyszło na jaw że moja frezarka mówiąc delikatnie jest za słaba mechanicznie. Projektując ją patrzyłem przede wszystkim na koszty wytworzenia dlatego oparłem cały napęd na paskach zębatych. To rozwiązanie sprawdza się w przypadku pisania po materiale, wypalania wzorów laserem, ale marnie sprawdza się przy okazji obróbki twardych lub trudnych w obróbce materiałów typu drewno czy chociażby pleksi. Pozatym moja maszyna okazała się odrobię mało precyzyjna właśnie przez napęd miękki jakim są pasy. Dlatego zapadła decyzja o stworzeniu mocniejszej maszyny która ma być pozbawiona tych wad a przy okazji pozwoli mi na dalszą naukę w tym temacie. Postanowiłem wykorzystać gotowe wzorce których jest mnóstwo w zasobach internetu. Sprzęt na bazie którego będę projektował swoją maszynkę kosztuje w granicach 650 zł w sklepach zagranicznych w polsce ponad 1000 zł. Będę projektował bo w moich planach pragnę wykorzystać części z poprzedniej CNC aby zmniejszyć koszty a poza tym wykorzystać te podzespoły do czegoś pożytecznego żeby nie zalegały w szufladach biurka. Nowe wcielenie mojej frezarki będzie oparte na ramie wykonanej z profili aluminiowych oraz napędzie opartym na śrubach trapezowych o średnicy 8 mm. Pozatym sprzęt dostanie nową elektronikę która będzie lepsza oraz ma obsługiwać poprawnie end stopy z czym miałem problem w starszej wersji mojego CNC. Uchwyt w moich planach ma być przygotowany pod ewentualny laser do grawerki.
Etap 1 - budowa ramy.
Rama jest wzorowana na mini frezarce 3018 która jest szczegółowo omówiona w zasobach internetu. Moja frezarka będzie znacznie zmodyfikowana żeby wyeliminować wady wspomnianego modelu. Do budowy ramy wykorzystam aluminiowy profil konstrukcyjny o przekroju 20x20 mm.. Do tego celu będę potrzebował: 5 szt. długości 360 mm 2 szt. długości 330 mm 2 szt. długości 220 mm Profile zostały przycięte na odpowiednią długość z dbałością o precyzję. Zostaną ze sobą połączone przy pomocy łączników aluminiowych w kształcie trójkąta o wymiarze
20x20 mm oraz wkrętów imbusowych z nakrętkami o średnicy 5 mm długości 10 mm. Podczas montażu zwróciłem uwagę że zachowując oryginalne wymiary nie wykorzystam maksymalnego pola roboczego na blacie frezarki. Wszystko zależy od rozmiarów osi Z i jej zasięgu pracy. W związku z tym przyjąłem wymiary montażu domyślne ale biorę pod uwagę możliwą późniejszą korektę. Na poniższym zdjęciu możemy zobaczyć skręconą ramę. Podczas montażu należy zwrócić szczególną uwagę na kąty, solidność skręcenia profili, oraz jakość wykonania. Od tego zależy jak bardzo będzie pracować precyzyjnie nasza maszyna. Wymiary jakie podałem nie są wymiarami bezwzględnymi, tylko przeniesionymi z frezarki 3018. Ostateczne wymiary zależą od nas i od tego co chcemy osiągnąć.
Dodatkowo dla wzmocnienia konstrukcji zostały przykręcone dwa wsporniki żeby usztywnić pionową ramę i przygotować na głowicę frezującą która, ma znaczną wagę. Wsporniki zostały wykonane na drukarce 3 D, kod STL do wydruku jest w linku.
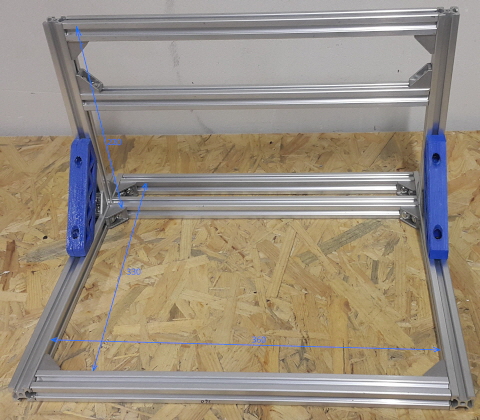
Element drukowane w technologii 3D
Podczas oczekiwania dostawy zamówionych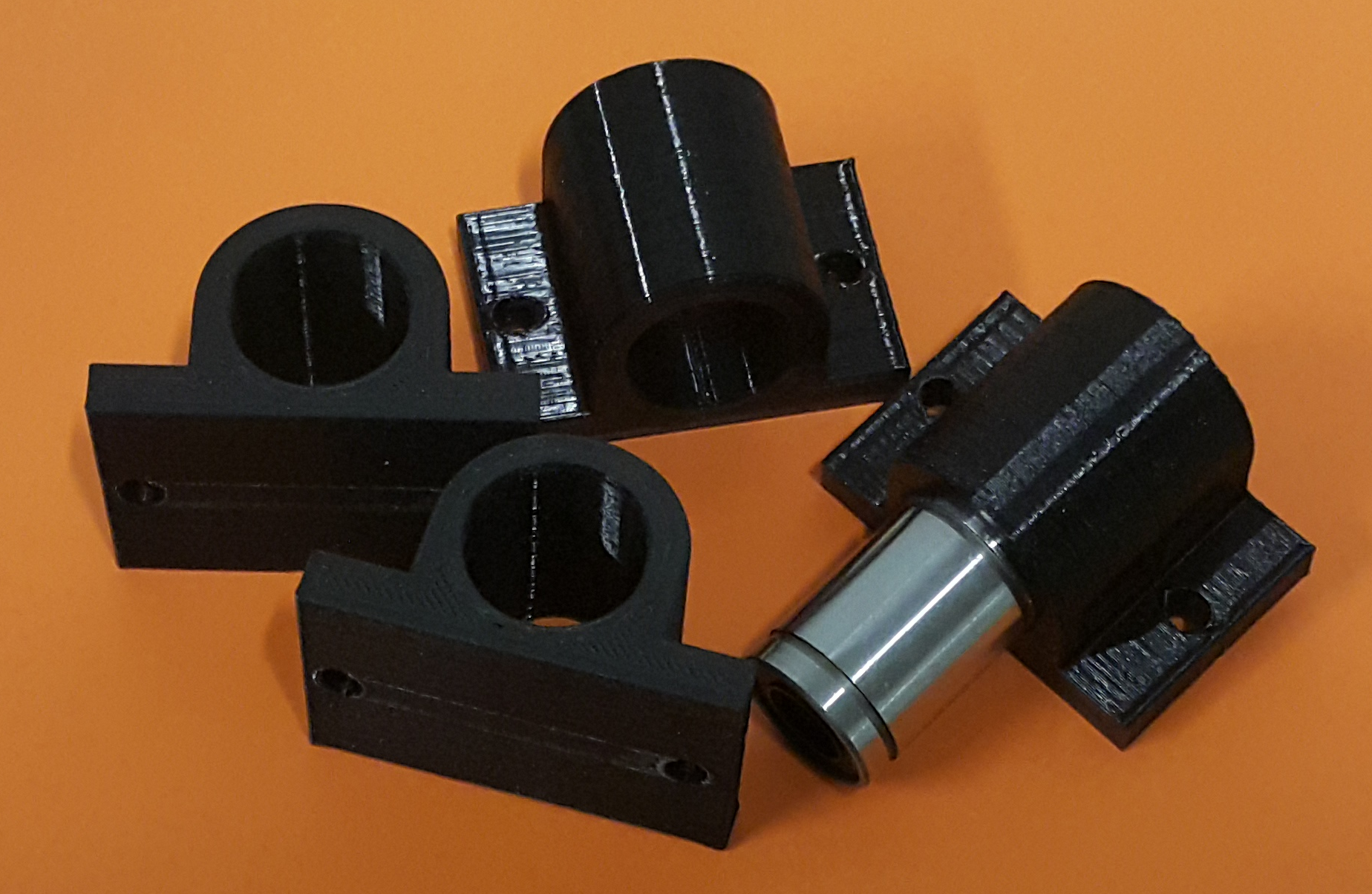 elementów postanowiłem zająć się kompletowaniem części które postanowiłem wykonać na drukarce 3 D. Do tych elementów zaliczają się między innymi obudowy łożysk liniowych które będą dzierżyć na swoich ramionach blat stołu roboczego. Wałki i łożyska będą w rozmiarze Fi 10 żeby w odróżnieniu od poprzedniczki doprowadzić do bardziej stabilnej i wytrzymałej konstrukcji a co za tym idzie pozyskać większe możliwości podczas frezowania w przyszłości. Wszystkie elementy o których mowa zostały wykonane na drukarce 3 D z materiału zwanego PLA 1,75.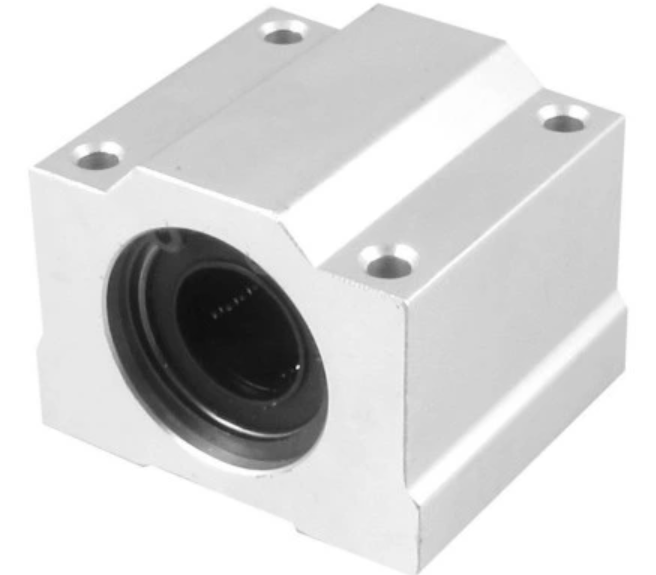 Co do parametrów wydruku to musicie dobrać je w zależności od sprzętu jakim dysponujecie. W związku z tym że nie każdy dysponuje technologią 3 D dla porównania zamieszczam orygilane elementy jakie zastępują. Na końcu dzisiejszego artykułu zamieszczam pliki z STL oraz rsdoc gdyby ktoś z was pragnął pójść moją drogą. Wszystkie elementy zostały zaprojektowane w programie „DesignSpark Mechanical v5. Kolejnym elementem który wykonałem jest wspornik wałka liniowego blatu stołu. Również jest przygotowany pod wałek fi 10. Element został nieznacznie wzmocniony w porównaniu do oryginału na którym się wzorowałem żeby zwiększyć stabilność stołu roboczego.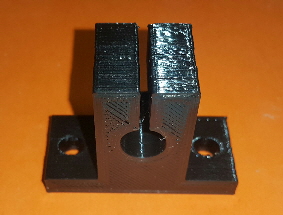 Ostatnim z elementów jakie dzisiaj zobaczyły światło dzienne są ozdobne zatyczki do profili aluminiowych. Nie mają one żadnego wpływu na konstrukcję frezarki ale poprawiają estetyke całego urządzenia.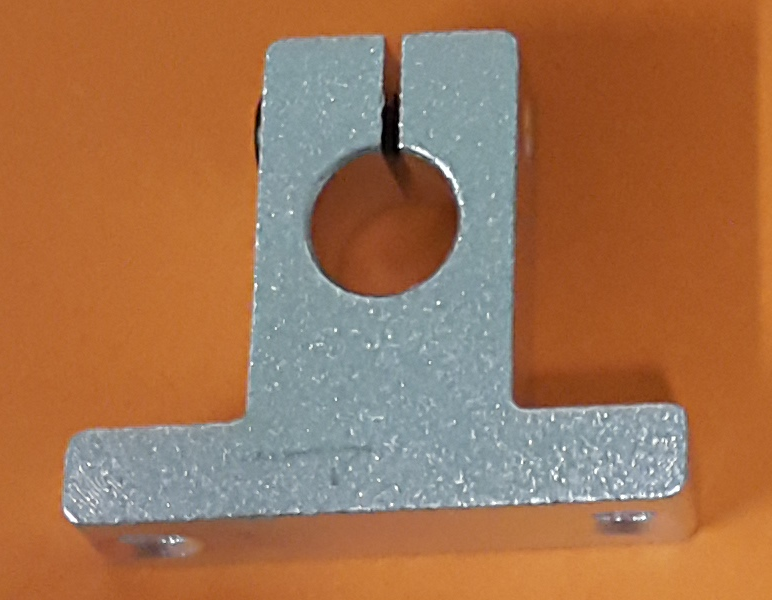
W zamieszczonych linkach znajdują się kody wykonanych elementów. Obudowa łożyska - stl, rsdoc Wspornik wałka - stl, rsdoc Zatyczka profilu - stl, rsdoc
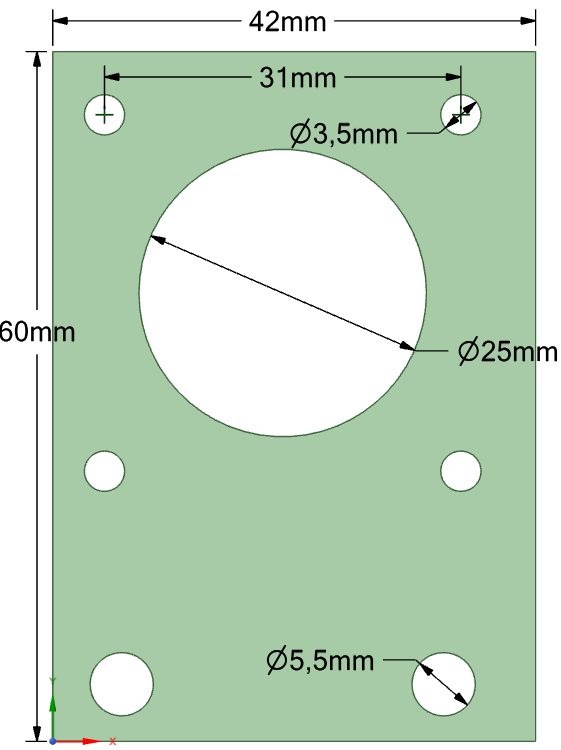
Obok na rysunku pokazane jest mocowanie silnika krokowego „Nema 17. Można kupić taki element gotowy. Ja wykonałem go z 2 mm ocynkowanej blachy stalowej. Potrzebujemy 2 sztuki do zamocowania silników osi X i Y. Zamieszczam również pliki do drukarki 3D. W tym przypadku przyjąłem grubość elementu wynoszącą 5 mm.
Mocowanie silnika Nema 17- stl, rsdoc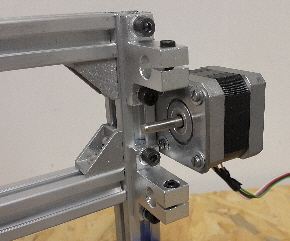
Moja mini – frezarka wzbogaciła się o kilka elementów. Zamontowałem w niej część przygotowanego osprzętu między innymi silniki, uchwyty pod wałki ślizgowe osi X oraz wałki i łożyska w obudowach osi Y.
Frezarka SNS złożona jest z wielu elementów. Dlatego naturalne jest że przyszła kolej na przygotowanie następnych części które składają się na całość urządzenia.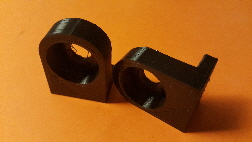 Zaprojektowałem i wydrukowałem na mojej niezawodnej drukarce kolejne elementy. A są to obudowy łożyska podtrzymującego śrubę napędową osi X i Y. W obudowach będą osadzone łożyska typu 608 RS które idealnie pasują do śruby ciągnącej. Wydrukowałem również mocowanie silnika krokowego Nema 17 do głowicy frezującej.
Będzie ono spajać silnik z łożem głowicy a także w swoich wnętrzach będzie przechowywać łożysko elastyczne które połączy silnik z śrubą napędową osi Z. Po ponad miesiącu doszedł w końcu uchwyt frezów który jest niezbędny do prawidłowego i precyzyjnego frezowania. Uchwyt został wyposażony w kilka wymiennych szczęk które dają możliwość zastosowania frezów o różnej grubości.
I jak zwykle zamieszczam pliki z kodami kolejnych elementów.Wykonałem również kostkę łączącą blat roboczy z trapezową śrubą napędową osi Y: rsdoc, stl Obudowa łożyska śruby ciągnącej: stl, rsdoc
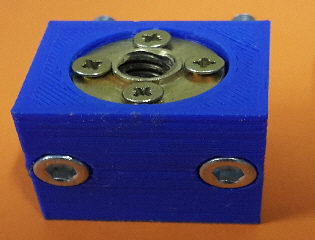 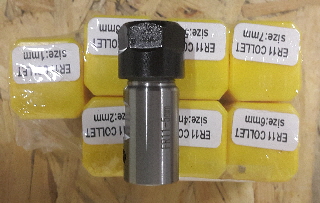
Wspornik silnika głowicy: stl, rsdoc
Jak można zobaczyć poniżej wyprodukowałem kolejny elementdo głowicy frezującej. Tym razem jest to uchwyt do zamocowania silnika wrzeciona frezującego. Jako ciekawostka dodam że został on podobnie jak wcześniejsze elementy wydrukowany z filamentu zwanego PLA. Czas wydruku to ponad 8 godzin przy rozsądnych parametrach wydruku. Cztery nadcięcia które widać w otworze mocowania silnika zostały przygotowane pod kątem zamocowania lasera.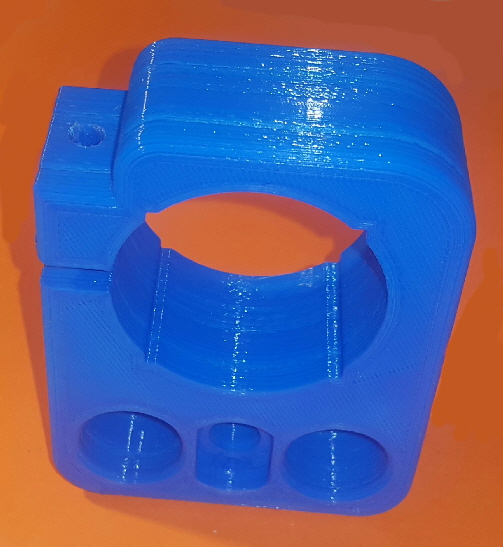
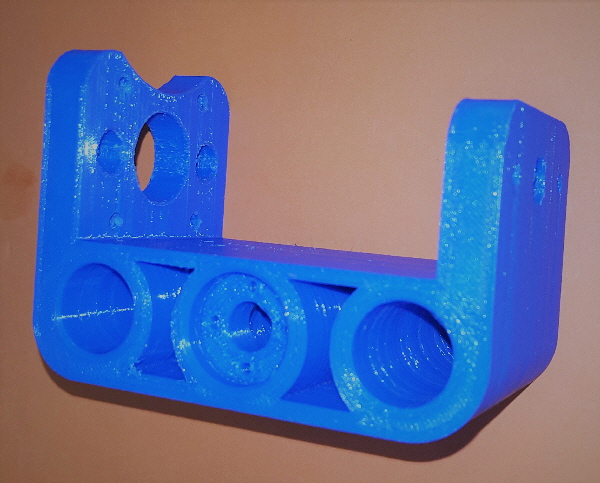
Głowica - stl, rsdoc
Kolejnym elementem jaki powstał w moim warsztacie jest wspornik uchwytu silnika głowicy (zdjęcie nad tekstem). Długo wahałem się z czego wykonać tą część. Rozpatrywałem dwa warianty. Wykonać z aluminium, przez co była by solidniejsza ale za razem kosztowna ewentualnie stworzyć ją w technologi 3D co prowadziło do spędzenia kilku godzin przy komputerze i powierzenia czarnej roboty drukarce. To rozwiązanie jest łatwiejsze mniej kosztowne, zaledwie kilka złot za filament i prąd, ale obarczone niepewnością czy wydruk z tworzywa wytrzyma obciążenia jakie będą występować podczas pracy frezarki. Ostatecznie stanęło na drugiej propozycji. Sprawdziło się w poprzednim ploterze to może i sprawdzi się w tym. Czas pokarze. Zresztą w maszynie na której się wzoruje uchwyt również został wykonany w tej technologi i jakoś daje radę. Jedyna różnica jest taka że moja konstrukcja jest znacznie solidniejsza. Jako ciekawostkę dodam że drukarka potrzebowała 14 godzin żeby stworzyć takie cudo. Ustawienia drukarki zostały ograniczone żeby skrócić czas pracy maszyny o 14 godzin. Tak dobrze liczycie, pierwotnie czas operacji został obliczony na 28 godzin pracy. Okupione to zostało jakością i wytrzymałością, ale cóż, coś za coś. Wziąłem się za montaż całej głowicy o czym po zakończeniu nie omieszkam się pochwalić. Podczas montażu trzeba zwrócić baczną uwagę na odpowiednie spasowanie łożysk wałków i innych elementów składających się na całość. Wspominam o tym żeby nie doprowadzić do niepotrzebnych naprężeń co mogło by osłabić całość urządzenia.
Zanim napiszę o montażu głowicy chciałbym zwrócić waszą uwagę na wsporniki blatu roboczego. Jak widać na zdjęciu u góry znacznie je pogrubiłem. Stopkę obudowy łożyska podniosłem o 10 mm. Dokonałem takiej modyfikacji w związku z tym żeby stół wynieść ponad wsporniki wałków oraz silnika osi Y. Dzięki takiemu zabiegowi frezarka będzie miała większe pole pracy.
Co do głowicy oczywiście nie obyło się bez drobnych kłopotów. Musiałem odrobinę zmodyfikować gniazdo mocowania nakrętki ciągnącej w uchwycie silnika ponieważ ta którą kupiłem okazała się trochę większa od otworu jaki przewidziałem na nią w projekcie wydruku. Poza tym montaż poszedł bez większych problemów. Zamontowałem głowicę na wałkach prowadzących osi X i prowizorycznie podłączyłem silnik do sterownika żeby ocenić efekty mojej pracy, co możecie zobaczyć na załączonym filmiku. Musiałem trochę zwiększyć prąd na drajwerze (wszystkie elementy maksymalnie spasowane) i po uruchomieniu posuwu przesmarować wałki oraz oś. Na wałku silnika zamontowałem nowy uchwyt do frezów. Temat głowicy frezującej uważam za zamknięty. Teraz kolej na montaż blatu roboczego oraz śrub trapezowych.
Kolejnym elementem który pojawił się na placu budowy to są śruby trapezowe o średnicy 8 mm które zostały wprowadzone do tulei ciągnących oraz połączone z sprzęgłami na silnikach. Drugi koniec został podparty wspornikiem uzbrojonym w łożysko 608. Wałki zostały przycięte na odpowiednią długość i zakończone plastykowymi skuwkami. Blat roboczy pierwotnie miał być wykonany z profila aluminiowego ale ostatecznie został wykonany z 15 mm sklejki przyciętej na wymagany wymiar. Koszt zakupu sklejki to tylko 7 zł na portalu Allegro co stanowi 15 część zakupu profila aluminiowego. Na powierzchni blatu wytrasowałem siatkę otworów które zostały wywiercone wiertłem fi 8 a następnie uzbrojone w gwintowane tulejki do drzewa. Na zakończenie blat został przykręcony do podwyższonych obudów łożysk ślizgowych i połączony z ciągadłem na śrubie trapezowej osi Y. To był ostatni element budowy mini frezarki ze strony mechanicznej. Pozostało wyposażyć urządzenie w elektronikę. Ale to będzie kolejny temat mojego serialu.
|